بهینه سازی اندازه دروازه و محل قرارگیری در قالب تزریق پمپ لوسیون تجزیه و تحلیل جریان قالب شامل یک فرآیند سیستماتیک شبیه سازی، تجزیه و تحلیل و تنظیمات طراحی است. در اینجا یک راهنمای گام به گام برای دستیابی به این بهینه سازی آورده شده است:
1. اهداف و معیارهای پروژه را تعریف کنید:
- با تعریف دقیق اهداف و معیارهای قالب تزریق پمپ لوسیون شروع کنید. عواملی مانند کیفیت قطعه، زمان چرخه، مصرف مواد و محدودیتهای هزینه را در نظر بگیرید.
2. جمع آوری داده های مواد:
- داده های دقیق مواد را برای رزین پلاستیکی خاص که در فرآیند قالب گیری تزریقی استفاده می شود، بدست آورید. این شامل شاخص جریان مذاب (MFI)، ویسکوزیته، خواص حرارتی، و سایر مشخصات مواد است.
3. ایجاد مدل:
- یک مدل سه بعدی دقیق از قسمت پمپ لوسیون و قالب تزریق، شامل حفره، هسته، کانال های خنک کننده و سیستم رانر ایجاد کنید. اطمینان حاصل کنید که مدل به طور دقیق شرایط تولید مورد نظر را نشان می دهد.
4. راه اندازی شبیه سازی:
- از نرم افزار تجزیه و تحلیل جریان قالب برای راه اندازی شبیه سازی استفاده کنید. پارامترهای فرآیند قالب گیری تزریقی، مانند فشار تزریق، پروفیل های دما، و نرخ های خنک کننده را تعریف کنید. مکان های دروازه و اندازه های اولیه دروازه را مشخص کنید.
5. اجرای اولیه شبیه سازی:
- شبیه سازی اولیه جریان قالب را با مکان ها و اندازه های دروازه انتخاب شده اجرا کنید. نتایج را تجزیه و تحلیل کنید، از جمله زمان پر شدن، توزیع فشار، خطوط جوش و مکان های تله هوا. هر گونه مشکل یا زمینه های بالقوه برای بهبود را شناسایی کنید.
6. تجزیه و تحلیل موقعیت دروازه:
- مناسب بودن مکان های دروازه انتخابی را ارزیابی کنید. عواملی مانند پر کردن متعادل حفره ها، اجتناب از عیوب زیبایی و به حداقل رساندن تاثیر خطوط جوش را در نظر بگیرید. در صورت نیاز مکان های دروازه را تنظیم کنید.
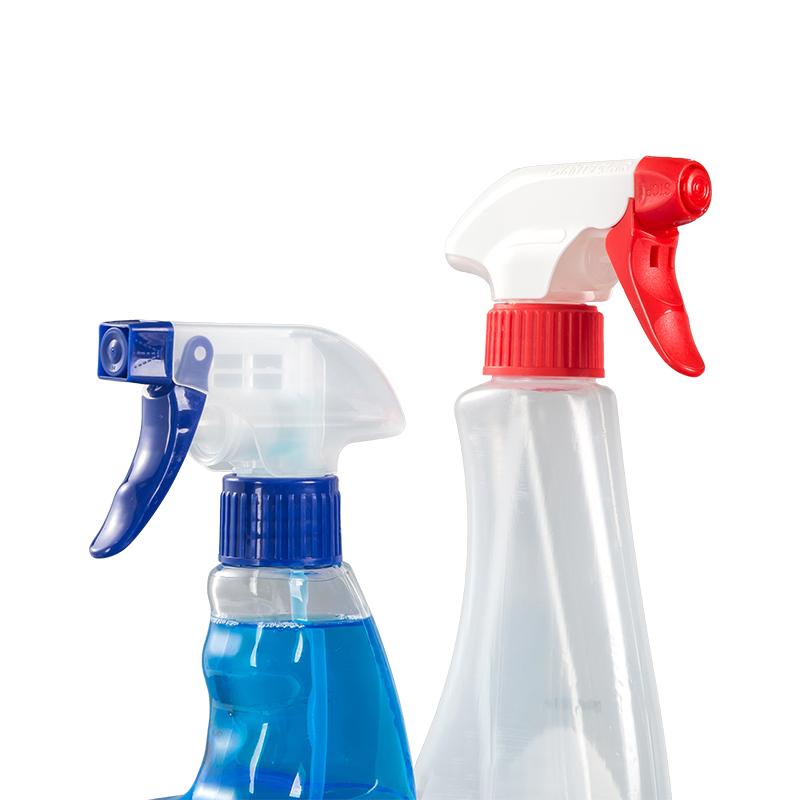
7. تجزیه و تحلیل اندازه دروازه:
- تأثیر اندازه گیت بر فرآیند تزریق را تجزیه و تحلیل کنید. در شبیه سازی های بعدی به تدریج اندازه دروازه را افزایش یا کاهش دهید تا اندازه بهینه ای را پیدا کنید که زمان پر کردن، فشار و جریان مواد را بدون ایجاد نقص متعادل می کند.
8. انتخاب نوع دروازه:
- بسته به نتایج تجزیه و تحلیل اندازه گیت، نوع گیت مناسب مانند گیت اسپرو، گیت لبه یا گیت فن را انتخاب کنید. نوع دروازه بر نحوه ورود مواد به حفره تأثیر می گذارد و می تواند بر کیفیت قطعه تأثیر بگذارد.
9. بهینه سازی سیستم Runner:
- طراحی سیستم دونده را برای اطمینان از توزیع یکنواخت مواد در تمام حفره ها بهینه کنید. ابعاد و تنظیمات دونده را برای به حداقل رساندن ضایعات مواد و افت فشار تنظیم کنید.
10. تجزیه و تحلیل کانال خنک کننده:
- تأثیر مکان و اندازه دروازه بر راندمان خنک کننده را ارزیابی کنید. اطمینان حاصل کنید که پیکربندی گیت انتخابی در اثربخشی کانال های خنک کننده تداخلی ایجاد نمی کند. در صورت لزوم محل کانال خنک کننده را تنظیم کنید.
11. شبیه سازی تکراری:
- انجام شبیه سازی های تکراری، انجام تنظیمات تدریجی در مکان ها و اندازه های دروازه بر اساس نتایج تجزیه و تحلیل. به اصلاح طرح ادامه دهید تا زمانی که معیارهای مورد نظر، مانند پر کردن متعادل و حداقل نقص، برآورده شود.
12. اعتبار سنجی نهایی:
- تجزیه و تحلیل جریان قالب نهایی را برای تأیید اندازه و مکان بهینه دروازه انجام دهید. تأیید کنید که طرح با اهداف و معیارهای از پیش تعریف شده پروژه مطابقت دارد.
13. مستندسازی و گزارشگری:
- نتایج را مستند کنید، از جمله پیکربندی گیت انتخابی، داده های شبیه سازی و هرگونه تنظیمات طراحی. گزارشی از خلاصه فرآیند بهینه سازی و نتایج آن تهیه کنید.